Rubber Running Track Repairs: Beginner’s Guide
5 April, 2024
Whether made for professional runners, occasional joggers, or just people walking by, rubber runways can be found everywhere – at stadiums, schools, and public parks; it can be a part of a running field, a pavement, or even a military construction. Rubber is a pretty versatile and durable material, suitable for countless applications and requiring relatively low maintenance. However, if damaged, it ought to be fixed as soon as possible. This article will delve into all the peculiarities of rubber running track repair and make a beginner’s guide for you.
Common Issues and Wear Patterns
Compared to other materials, like asphalt or concrete, rubber demonstrates superior durability, being less likely to form cracks or potholes. Nevertheless, rubber can’t last forever, likely forming cracks or other track surface irregularities, such as bumps, warps, micro-pits, or loose granules. Most of these effects come naturally due to extensive foot traffic, which is ordinary for running tracks, and temperature and moisture level fluctuations. In addition, prolonged exposure of rubber to direct sunlight and severe weather conditions can cause it to fade, losing color unevenly.
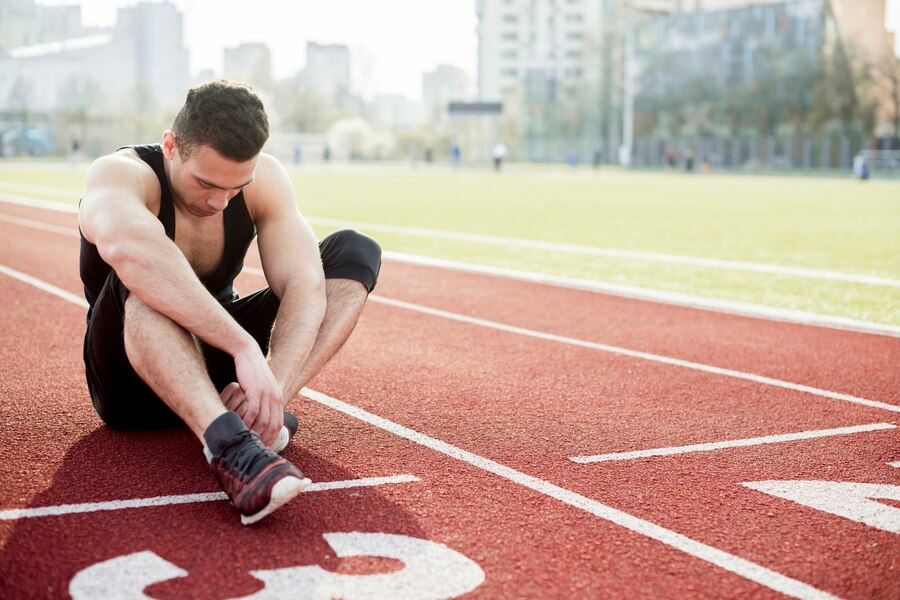
Preparing for Repair
No need to panic; almost all the defects and damages can be fixed if prepared correctly. Firstly, you need to assess the situation, paying extra attention to the following aspects:
- Type of damage.
- The size of the damaged area.
- The general state of the covering (how wet and hot it is).
After thoroughly evaluating the situation, it’s time to pick the tools and materials that you will need for the repairs.
Tools and Materials Needed
First, you will need a repair kit of rubber granules to replace the damaged ones and the polyurethane adhesive needed to glue them. Although this process doesn’t require any fancy accessories, some more tools will be in handy:
- Utility knife – used to widen small cracks for better adhesion.
- Brush – every rubber track repair kit includes binder (adhesive), which needs to be applied to the edges of the damaged area.
- Scraper – it can help remove debris and loose granules, as well as even out the surface.
- Pressure washer – rubber must be clean before filling in the damaged areas. Hence, a pressure washer is a must to get rid of all the dirt or debris left after the scraper.
- Releasing agent – applying it to the scraper/level during the process will help you keep fresh rubber everywhere.
However, some factors detract from the pros of rubber covering:
- Limited design options – although rubber can come in various colors and textures, its variety and appeal are limited compared to pavement or stone.
- Price – rubber can be a rather costly choice, averaging at approximately $8-16 per square foot.
Safety Precautions
To avoid hurting yourself in the process of your running track repair, follow these recommendations:
- Avoid eye or bare skin contact with the adhesive.
- Use personal protective equipment, such as goggles and gloves the whole time.
- If the running track is indoors, ensure proper ventilation and protection of breathing ways to avoid inhalation of fumes.
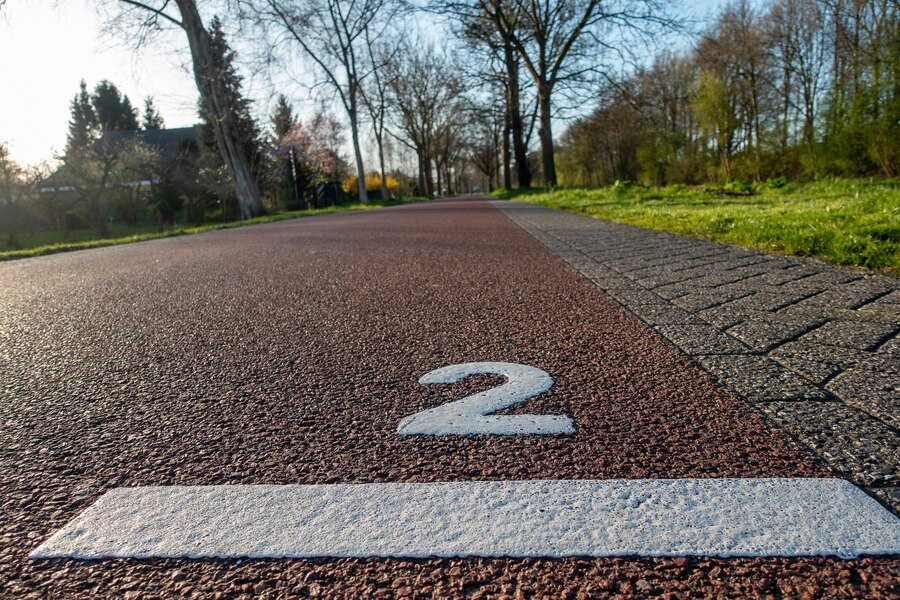
Repair Running Track Step-By-Step
With all the preparations done, let’s start repairing your rubber running track and discuss it step-by-step.
1. Cleaning and Preparing the Surface
If the crack you are trying to fill in is too small and is in the surface layer, consider using a utility knife to widen it. Try to cut out a square-like shape; it will be easier to clean and fill in. After it is done, use a scraper and a pressure washer to remove all the dirt, loose granules, and debris. When the surface is clean, give it some time to completely dry. This way, you will be confident that no mold, mildew, or other weeds will develop underneath and that nothing will diminish the effect of the adhesive.
2. Repairing Small Cracks and Cuts
Instruction provided by a rubber repair kit manufacturer: after your damaged surface is clean and dry, apply some of the binder to the edges of the damaged area with a brush. After, mix the rubber granules and the adhesive from the kit. You can use a stick or even your own hands; just make sure to wear protective gloves. After the granules and the binder are mixed, pour them into the damaged area, trying to have it ¼ inch higher than the rest of the surface (it helps prevent material voids in the patch). After the patch is filled, even it through the whole area using your scraper, applying a releasing agent after every two or three swipes to ensure fresh rubber doesn’t stick. After smoothing out your patch and ensuring the new material doesn’t overlap with the existing surfacing, let it rest for 24 hours before using the surface.
3. Patching Larger Damages
The process of patching larger damaged areas is similar to smaller cracks and torn-outs. Yet, there are a few different points to address here:
- Amount of material – a larger hole means more material is required to fill them in. Consult with the kit providers to determine the amount of rubber and adhesive required for the area and depth of your damaged surface.
- Preparation – inspect the nearby parts of the surface to determine if there are any signs it may also become damaged soon.
- Tools – use levels (measuring tools) to level the rubber mass.
- Curing time – the larger the damaged area is, the longer it will take to fully dry out before being available for use again.
4. Resurfacing Techniques
Resurfacing is the final option you can go for if the damaged area is extensive. In this case, removing the whole section of the running track and replacing it entirely is recommended. The main pros of going for track resurfacing are:
- Consistent result – a larger area means that there will not be a random patch of a different color/shade in your running track.
- Safety – even a tiny crack or tear-out can indicate more severe damage underneath the rubber. Replacing the whole section helps prevent further damage in the same area.
However, there are also cons of resurfacing:
- Cost – if you decide to resurface a section or even the whole running track, it will require way more materials, not to mention that it should be done by professionals, coming with extra expenses.
- Time and effort – if track resurfacing is done DIY or by professionals, it will still come with more effort and energy than even fixing a big crack, which can usually be done in under a day.
5. Professional Repair Options
When it comes to more severe damage, like extensively damaged areas, warping, bumping, or fading, one of the most optimal options is to address professional repair services with years of experience. Though repairing your running track professionally can be pretty pricey, it is the best idea due to the following factors:
- Result – professional repair services ensure the best result for any installation or repair project due to their approaches and processes, such as laser leveling. Moreover, most companies provide a long-lasting warranty.
- Quality of materials – certain repair services collaborate with suppliers directly, meaning they can have better materials for your needs.
Regular Maintenance Tips
To avoid the need for constant repairs of your rubber running track, follow these maintenance tips:
- Visual inspections – regularly inspect your rubber running track to detect any defect formation as soon as possible to fix them immediately.
- Cleaning – rubber requires occasional cleaning to prevent the build-up of debris, which can wreck the integrity of the surface or lead to other defects.
- Avoid irritators – although rubber is exceptionally durable to shock and almost any weather condition, it can be vulnerable to cuts and certain chemicals, which can eat through the granules and the adhesive, so steer clear of them.